Czym jest system konstrukcji paneli SIP?
SIPs, also known as structural-insulated panels, became popular as an energy-efficient building material even in the middle of the last century. They comprise two outer layers of oriented strand board (OSB), MgO boards or GFB (gypsum fiber boards), with a foam core in between. The foam core is usually made of expanded polystyrene (EPS) and polyurethane (PUR), providing excellent insulation properties.
Jakie są zalety budownictwa SIP?
- Wyjątkowa efektywność energetyczna: Panele termoizolacyjne są zaprojektowane tak, aby zapewniać doskonałą izolację, obniżając koszty energii i tworząc bardziej komfortowe warunki życia.
- Doskonałe wsparcie strukturalne, potwierdzone przez ETAG.
- Faster construction times. SIP panels are pre-fabricated, and the house can be quickly assembled on-site, reducing time, labor costs, and other fees.
- Proces produkcji paneli SIP generuje mniej odpadów materiałowych niż tradycyjne metody. Panele termoizolacyjne są wykonane z materiałów, które nie emitują szkodliwych gazów ani chemikaliów.
- Panele konstrukcyjne i izolacyjne mogą być używane do tworzenia szerokiego zakresu nowoczesnych pomysłów budowlanych. Mogą być również używane zarówno do domów mieszkalnych, jak i nieruchomości komercyjnych, spełniając specyficzne potrzeby projektu.
Aby rozpocząć produkcję i być bardziej konkurencyjnym, musisz kupić profesjonalne maszyny do produkcji wysokiej jakości SIP. Jesteśmy doświadczonym dostawcą kompletnego zestawu urządzeń do produkcji paneli warstwowych, oferującym maszyny o różnych poziomach automatyzacji i cenach odpowiednio.

Standardowy zestaw maszyn składa się z:
- Maszyny do laminowania i prasowania paneli;
- Maszyny do cięcia i rowkowania paneli;
- Maszyny pomocnicze - podnośniki, rdzeniarki, kruszarki, narzędzia do pakowania, znakowania i pomiaru.
Zalecamy użycie dwóch głównych rodzajów kleju poliuretanowego:
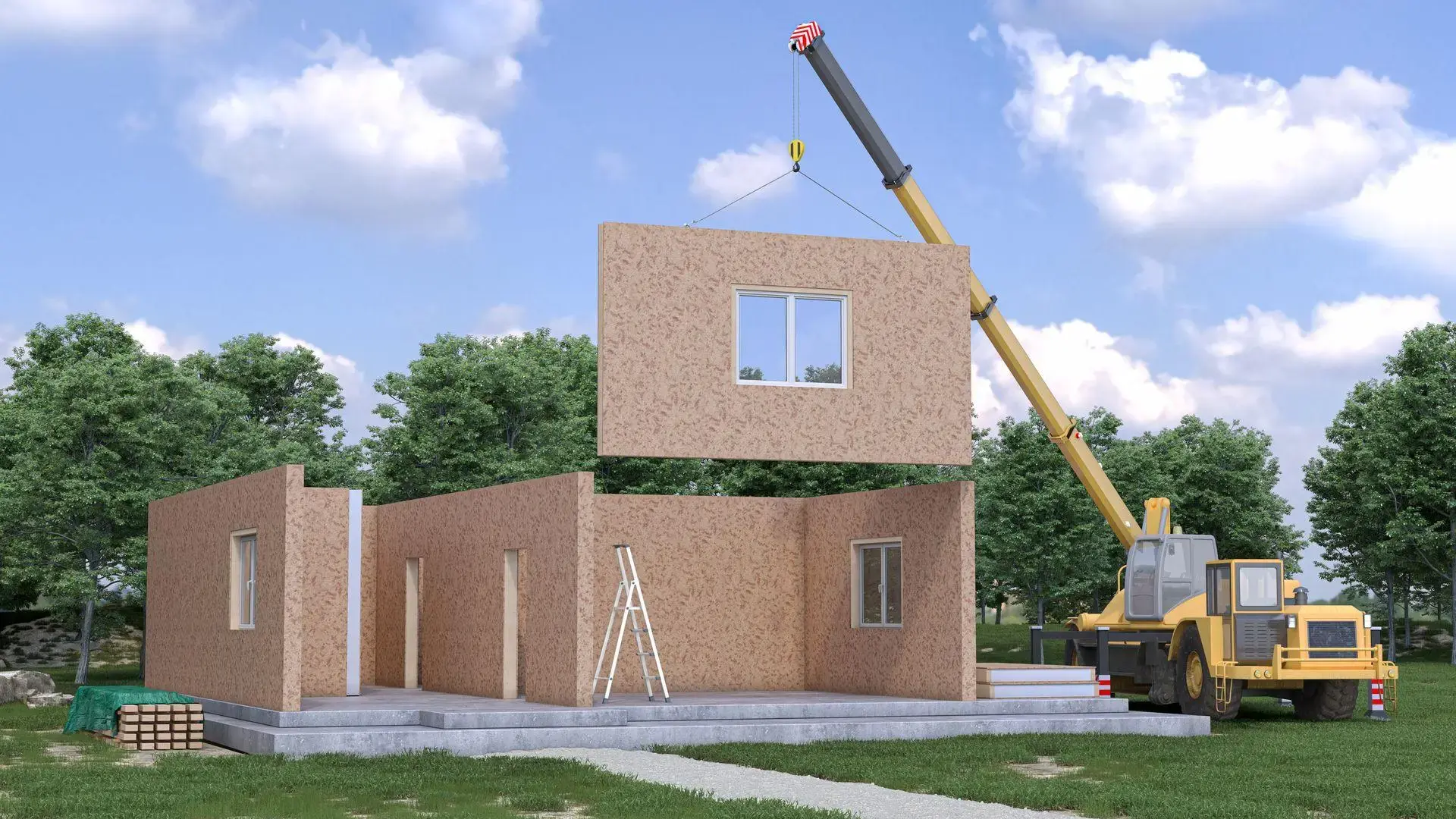
Proces produkcji paneli SIP to kluczowa i skomplikowana procedura, która zapewnia wysoką jakość naszych produktów. Obejmuje kilka kluczowych kroków, które dokładnie przestrzegamy, aby dostarczyć najwyższej jakości wyniki:
- Projektowanie domu w celu tworzenia planów klejenia, cięcia, montażu oraz wybór rodzajów elementów łączeniowych zgodnie z wymaganą nośnością paneli ściennych, dachowych lub podłogowych.
- Przygotowanie materiałów i kontrola jakości.
- Łączenie paneli;
- Cięcie paneli;
- Wykonywanie rowków połączeniowych w rdzeniu panelu;
- Oznaczanie paneli zgodnie z planem cięcia i pakowanie ich do dostarczenia;
Po wyprodukowaniu zestawu domu kolejnym krokiem jest montaż domu. Może to być wykonane wewnątrz fabryki lub na zewnątrz, bezpośrednio na placu budowy, w zależności od wymagań projektu.
Proces laminowania paneli.
Chcemy przedstawić niektóre z głównych typów urządzeń do produkcji paneli SIP, ale jesteśmy otwarci na omawianie indywidualnych zapytań klientów.
Półautomatyczna linia produkcyjna SIP jest wyposażona w maszynę do nakładania kleju PUR 1-C Gluestream SPL-9 oraz kilka pras typu C.
Maszyna do nakładania kleju może być używana z platformą stacjonarną lub ruchomą.
Stosy paneli są montowane w prasach typu C. Rozładunek płyt odbywa się za pomocą wózka widłowego.
How do we calculate the production capacity of the SIP panels production line, and how do we choose the PUR glue?
One-component PUR glue has two main parameters to calculate the SIP manufacturing line’s capacity:
- OJT – Open Joint Time (max time open to air), which is the time of assembling a stack of the boards in the press.
- PT – Czas prasowania, czas wymagany do prasowania.
The glue parameters are calculated if the temperature in the production facility is 20℃-25℃.
10–15 minut potrzebujemy na złożenie dziewięciu paneli SIP o grubości 170 mm w prasie;
- potrzebujemy kleju z 15-minutowym OJT.
- PT wynosi około 40 minut.
Możesz zobaczyć harmonogram produkcji SPL-9 z 4 prasami w 8-godzinnej zmianie.
W rzeczywistej produkcji możemy użyć współczynnika redukcji 0,8.
261*0,8=209 płyt na zmianę.
Personel to dwóch operatorów i jeden kierowca wózka widłowego.
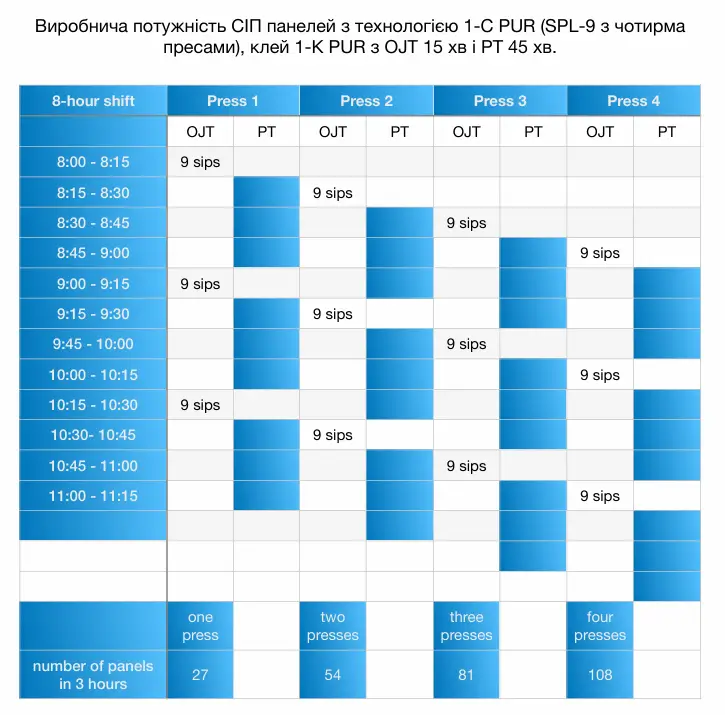
Linia produkcyjna paneli warstwowych SPL-2 z dwoma prasami portalowymi składa się z następujących modułów:
- Stacjonarny portal do nakładania kleju z automatycznie podnoszoną głowicą.
- Stacja pomp.
- Ruchomy wózek, na którym montowany jest stos płyt.
- Dwie prasy portalowe (maks.).
- Podnośnik próżniowy służy do załadunku materiałów na wózek (opcjonalnie).
- Rozładunek stosów odbywa się za pomocą wózka widłowego.
Wydajność produkcji – maks. 100 płyt na zmianę.
Personel – dwie osoby (jedna z nich jest jednocześnie operatorem wózka widłowego).
Jeśli potrzebujesz mniejszej zdolności produkcyjnej, wybierz maszynę do produkcji SIP SPL-1 z jedną prasą
Linia produkcyjna paneli warstwowych, SPL-10M, składa się z następujących modułów:
- Ruchomy portal do nakładania kleju z automatycznie podnoszoną głowicą.
- Stacja pomp.
- Przenośnik rolkowy z lub bez podnośnika nożycowego.
- Platforma dystrybucyjna do dostarczania paneli do i z pras.
- Od jednej do sześciu pras portalowych.
- Podnośnik próżniowy do załadunku materiałów (opcjonalnie).
- Rozładunek stosów odbywa się za pomocą wózka widłowego.
Wydajność produkcji wynosi 50 – 250 płyt na zmianę, w zależności od liczby pras.
Personel – dwie osoby (jedna z nich jest jednocześnie operatorem wózka widłowego)
SPL-10M może być również częścią w pełni automatycznej linii produkcyjnej paneli SIP, która jest wyposażona w cztery prasy i automatyczny portal montażowy.
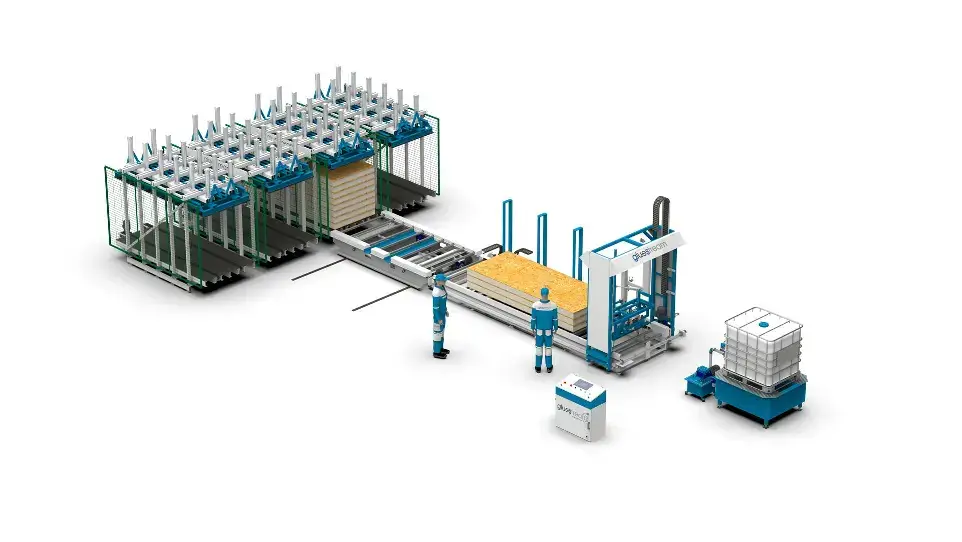
W pełni automatyczna linia produkcyjna paneli warstwowych ASPL 3.1.BFT
Sprzęt jest przeznaczony do automatycznego laminowania paneli SIP.
Linie produkcyjne Jumbo SIP
Intencja przeniesienia jak największej liczby procesów do fabryki staje się ekonomicznie praktyczna.
Czasami dostęp do potrzebnych materiałów w Twoim regionie jest ograniczony, dlatego stworzyliśmy proces technologiczny do produkcji paneli SIP w dużym formacie, które mogą być używane do tworzenia gotowych ścian, dachów i podłóg w fabryce.
Istnieje kilka sposobów, aby to zrobić.
Proces cięcia paneli SIP
Po stworzeniu planu cięcia dostarcza on ważnych informacji na temat pozycjonowania panelu na stole piły, w tym liczby elementów do cięcia, głębokości rowków połączeniowych i kątów obróbki. Dokładne przestrzeganie planu pozwala producentom zminimalizować straty materiału i zmaksymalizować wydajność obróbki płyt. Może to prowadzić do znacznych oszczędności kosztów i zwiększenia produktywności w produkcji.
Uniwersalna półautomatyczna piła do paneli SIP FPS-900
Jednym z najważniejszych narzędzi do obróbki płyt jest piła panelowa SIP FPS-900. Ta piła jest specjalnie zaprojektowana do cięcia paneli o grubości do 300 mm.
Piła może być używana do wszystkich cięć od 0 do 45 stopni.
Dodatkowo piła panelowa posiada automatyczny system pomiaru długości, który ustawia operator. Ta funkcja pomaga zapewnić precyzję i dokładność w procesie, zmniejszając odpady i poprawiając wydajność.
Piła FPS-900 występuje w dwóch modyfikacjach, aby dostosować się do unikalnej logistyki każdego zakładu produkcyjnego.
Pierwsza modyfikacja to FPS-900.BC.AM, posiada system przenośnika taśmowego, który dostarcza i ustawia panele w obszarze roboczym. Ta modyfikacja jest wyposażona w automatyczny system pomiarowy i system pozycjonowania paneli.
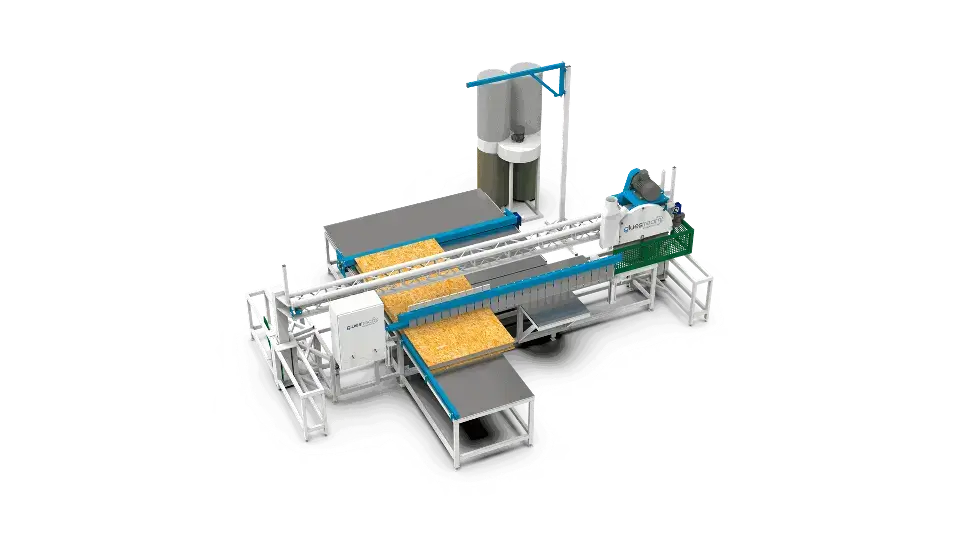
Druga modyfikacja piły SIP, FPS-900.ST.AM, nie posiada systemu przenośnika taśmowego. Zamiast tego pracownicy muszą ręcznie umieścić panel na stole i docisnąć go do belki pomiarowej, która jest umieszczona w pozycji cięcia. Po cięciu, kawałki paneli są automatycznie zwracane do strefy załadunku za pomocą belki. Powierzchnia stołu jest pokryta stalą nierdzewną, co zapewnia trwałość i łatwość czyszczenia.
Proces rowkowania paneli SIP
Rowkowanie paneli SIP maszyna FPS-400 jest niezbędnym narzędziem do tworzenia rowków połączeniowych w rdzeniu SIP wykonanych z materiałów takich jak EPS, spieniony PU i PIR. Każdy zestaw narzędzi tnących jest projektowany zgodnie z wymaganiami klientów i projektami rowków połączeniowych, zapewniając precyzyjne i dokładne rowki. Głowica tnąca porusza się wzdłuż precyzyjnych prowadnic, a pneumatyczny system mocowania zapewnia, że płyta jest mocno umieszczona na stole roboczym.
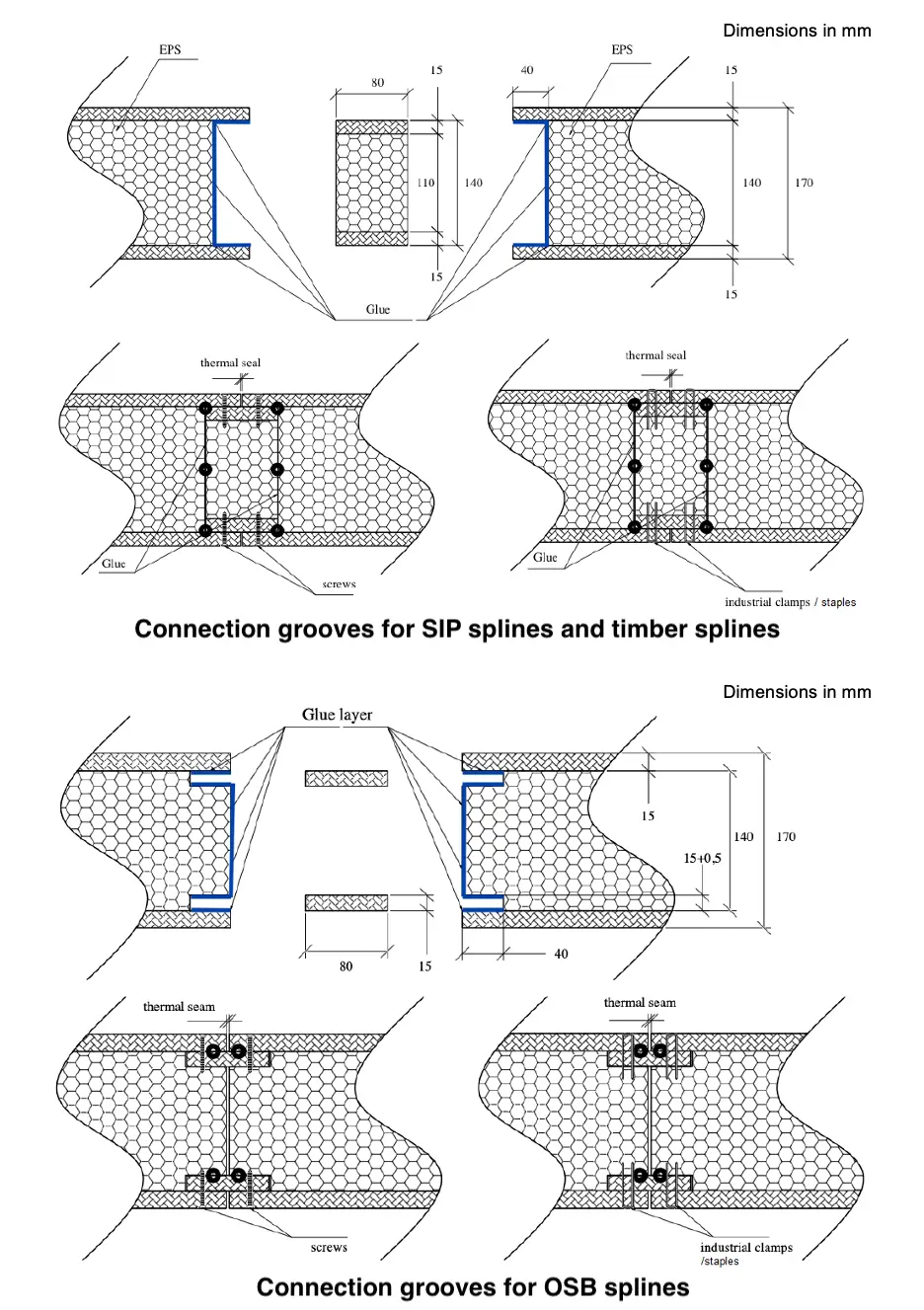
Powierzchnia robocza stołu jest pokryta stalą nierdzewną, co zapewnia trwałość i łatwość czyszczenia. Maszyna jest wyposażona w system hamulca elektrycznego i mechaniczny system ochrony rąk, co zapewnia bezpieczeństwo podczas pracy. Parametry rowkowania są ustawiane na konsoli sterującej, co usprawnia proces konfiguracji i zapewnia dokładność.
Proces cięcia płyt EPS
Wszystkie materiały, z wyjątkiem płyt EPS, są dostarczane w stanie gotowym do użycia. Płyty EPS są wykonane z bloków EPS, ponieważ większość dostawców płyt EPS nie może zagwarantować dokładności grubości płyt EPS, dlatego musimy sami ciąć bloki przed klejeniem paneli.
Grubość płyt EPS jest równa grubości połączenia drewno/element plus 2 mm.
If a connection element is 140 mm thick, the EPS board must be 142mm to insert a connection element into the panel.
Możemy zaoferować dwa rodzaje maszyn:
Proces montażu Jumbo-SIP
Jumbo-SIP — to, co nazywamy dużymi panelami, używanymi jako gotowe ściany, podłogi lub panele dachowe. Czasami zwiększenie liczby procesów produkcyjnych w fabryce jest ekonomicznie efektywne, a Gluestream rozwija technologię domów prefabrykowanych.
Możemy zaoferować wiele rodzajów stołów montażowych, stołów obrotowych i przechylających, przenośników i manipulatorów.