What is a SIP panel construction system?
SIPs, also known as structural-insulated panels, became popular as an energy-efficient building material even in the middle of the last century. They comprise two outer layers of oriented strand board (OSB), MgO boards or GFB (gypsum fiber boards), with a foam core in between. The foam core is usually made of expanded polystyrene (EPS) and polyurethane (PUR), providing excellent insulation properties.
What are the advantages of the SIPs building?
- Exceptional energy efficiency: Sandwich panels are designed to provide superior insulation, reducing energy costs and creating more comfortable living conditions.
- Excellent structural support, proved by ETAG.
- Faster construction times. SIP panels are pre-fabricated, and the house can be quickly assembled on-site, reducing time, labor costs, and other fees.
- The SIPs production process produces less wasted materials than traditional methods. Sandwich panels are made with materials that do not emit harmful gases or chemicals.
- Structured insulated panels can be used to create a wide scope of modern building ideas. They can also be used for both living houses and commercial properties, meeting the project’s specific needs.
To start production and be more competitive, you must buy professional machinery for high-quality SIP manufacturing. We are an experienced supplier of a complete sandwich panel production set of equipment, offering machinery with different levels of automation and prices correspondingly.

Standard machinery set consists of:
- Panel laminating and pressing machinery;
- Panel cutting and grooving machinery;
- Auxiliary machinery - lifters, core cutters, crushers, packing, marking, and measuring tools.
We recommend using two main types of polyurethane glue:
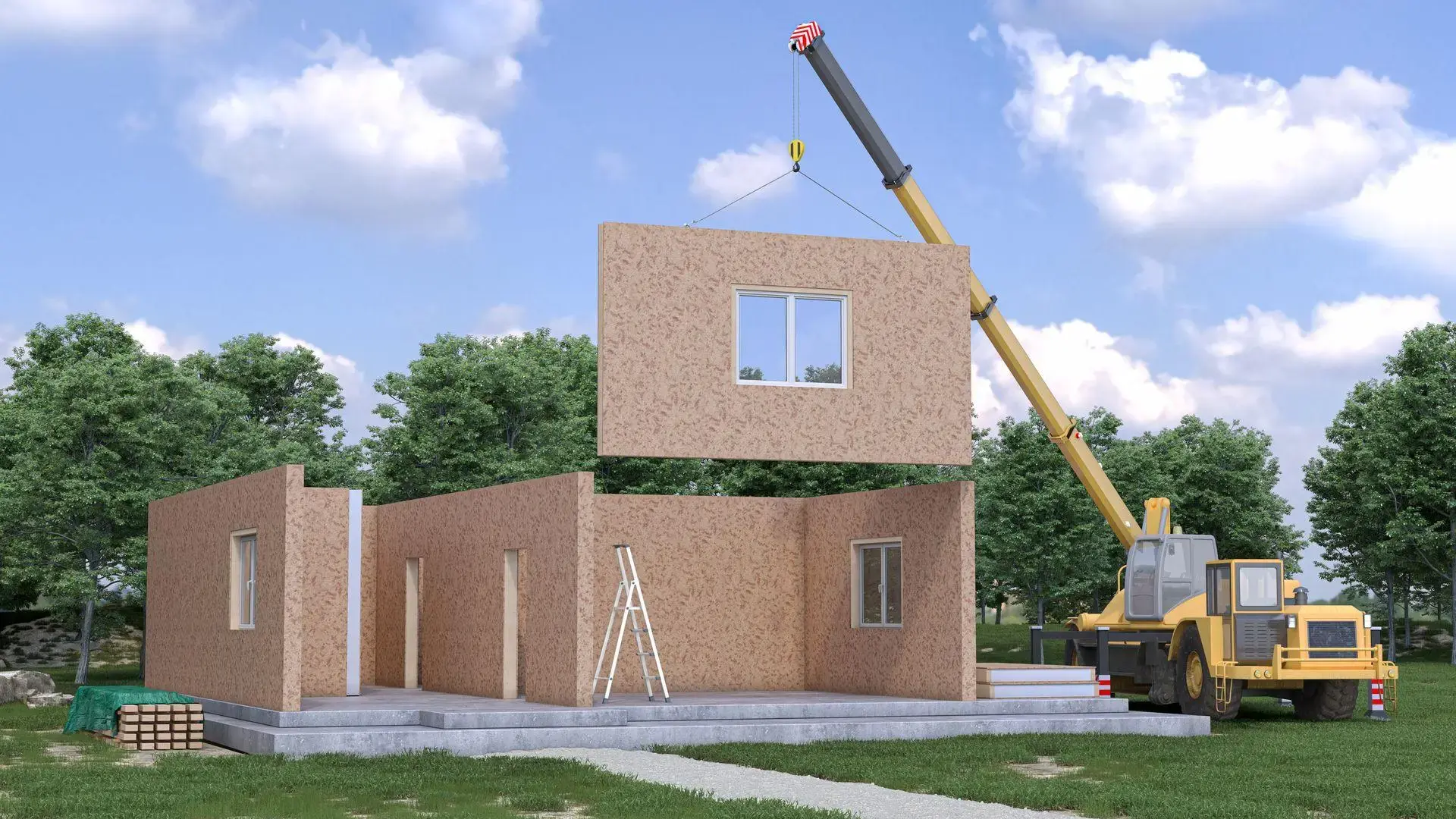
The SIPs manufacturing process is a crucial and intricate procedure that ensures the high quality of our products. It involves several key steps that we meticulously follow to deliver top-notch results:
- Designing the house for creating gluing, cutting, assembling plans, and choosing the types of connection elements according to the required loading capacity of the wall, roof, or floor panels.
- Material preparation and quality control.
- Bonding the panels;
- Panels' cutting;
- Making the connection grooves in the panel's core;
- Marking the panels under the cutting plan and packing them to deliver;
Once the house kit is produced, the next step is to assemble the house. This can be done either inside the factory or outside, directly on the construction site, depending on the project requirements.
Panel laminating process.
We want to present some of the main types of SIP panel manufacturing equipment, but we are open to discussing individual customer requests.
The semiautomatic SIPs production line is equipped with 1-C PUR glue-applying machine Gluestream SPL -9 and several C-type presses.
The glue-applying machine can be used with a stationary or movable platform.
The stacks of panels are assembled in the C-type presses. Unloading the boards occurs with a forklift.
How do we calculate the production capacity of the SIP panels production line, and how do we choose the PUR glue?
One-component PUR glue has two main parameters to calculate the SIP manufacturing line’s capacity:
- OJT – Open Joint Time (max time open to air), which is the time of assembling a stack of the boards in the press.
- PT – Pressing Time, the time required to press.
The glue parameters are calculated if the temperature in the production facility is 20℃-25℃.
10–15 minutes we need to assemble nine 170mm thick SIPs in the press;
- we need glue with 15 min OJT.
- PT is approximately 40 min.
You can see a production schedule of SPL-9 with 4 presses in an 8-hour shift.
In actual production, we can use a reduction factor of 0,8.
261*0,8=209 boards per shift.
Personal is two operators and one forklift driver.
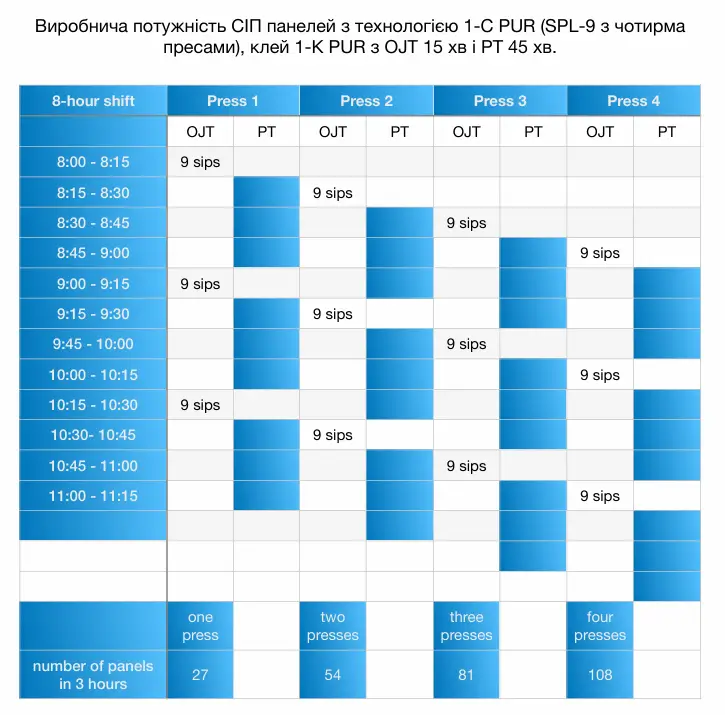
Sandwich panel production line SPL-2 with two portal presses consists of the following modules:
- A stationary adhesive-applying portal with an automatically lifted head.
- Pump station.
- A movable carriage, where the stack of the boards is assembled.
- Two portal-type presses (max).
- The vacuum lifter is used to load materials on the carriage (optional).
- Unloading the stacks occurs with a forklift.
Production capacity – max.100 boards per shift.
Personal – two people (one is a forklift driver concurrently).
If you need lower production capacity, the SIP
manufacturing machine SPL-1 with one press is your choice
Sandwich panel production line, SPL-10M, consists of the following modules:
- A movable adhesive-applying portal with an automatically lifted head.
- Pump station.
- A roller conveyor with or without scissors lift.
- A distribution platform, to deliver the panels in and out of presses.
- One to six portal-type presses.
- A vacuum lift, to load materials (optional).
- Unloading the stacks occurs with a forklift.
Production capacity is 50 – 250 boards per shift, depending on the number of presses.
Personal – two people (one of them is a forklift driver concurrently)
SPL-10M can also be part of the fully automatic SIP panel production line, which is equipped with four presses and an automatic assembling portal.
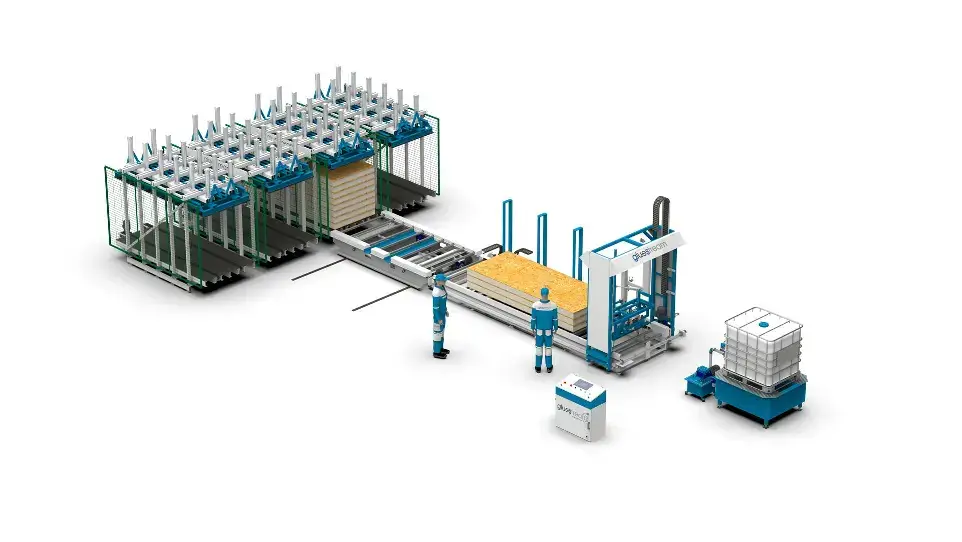
Fully automatic sandwich panel production line ASPL 3.1.BFT
The equipment is intended to laminate the SIPs automatically.
Jumbo SIP manufacturing lines
The intention to move as many processes as possible to the factory becomes economically practical.
Sometimes, access to the needed materials in your region is limited, so we created a technological process for producing big-format SIP panels that can be used to create ready-made walls, roofs, and floors in the factory.
There are a few ways to do it.
SIPs cutting process
Once a cutting plan has been created, it provides important details on positioning the panel on the saw table, including the number of elements to be cut, the depth of the connection grooves, and the processing angles. By precisely following the plan, manufacturers can minimize material waste and maximize efficiency in board processing. This can lead to significant cost savings and increased productivity in manufacturing.
Universal semiautomatic SIPs panel saw FPS-900
One of the most important tools for board processing is the SIP panel saw FPS-900. This saw is specifically designed to cut panels with a thickness of up to 300 mm.
The saw can be used for all cuts from 0 to 45 degrees.
Additionally, the panel saw features an automatic system for measuring length, which the operator sets. This feature helps to ensure precision and accuracy in the process, reducing waste and improving efficiency.
The saw FPS-900 comes in two modifications to accommodate the unique logistics of each production facility.
The first modification is FPS-900.BC.AM, features a belt conveyor system that delivers and positions the panels in the working area. This modification is equipped with an automatic measurement system and a panel positioning system.
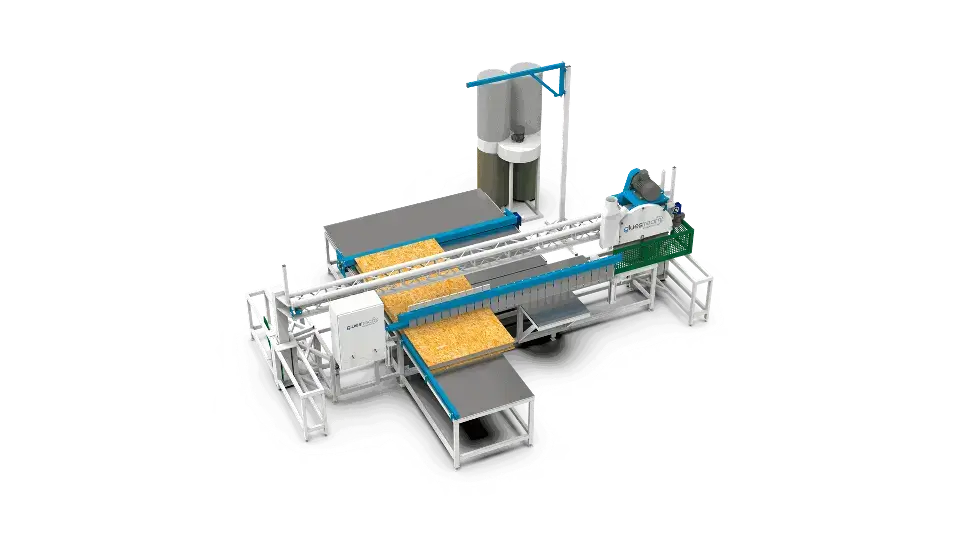
The second modification of the SIP saw, FPS-900.ST.AM, does not feature a belt conveyor system. Instead, workers must manually place the panel on the table and press it to the measuring beam, which is placed in the cutting position. After cutting, the pieces of the panels are automatically returned to the loading area with a beam. The table’s surface is covered with stainless steel to ensure durability and easy clean-up.
Grooving process of SIP panels
SIP panel grooving machine FPS-400 is an essential tool for creating connection grooves in the core of SIPs made of materials such as EPS, foamed PU, and PIR. Each set of cutting tools is designed according to the customers’ requirements and the connection grooves’ designs, ensuring that the grooves are precise and accurate. The cutting head is moved along precise guides, and the pneumatic clamping system ensures the board is firmly positioned on the working table.
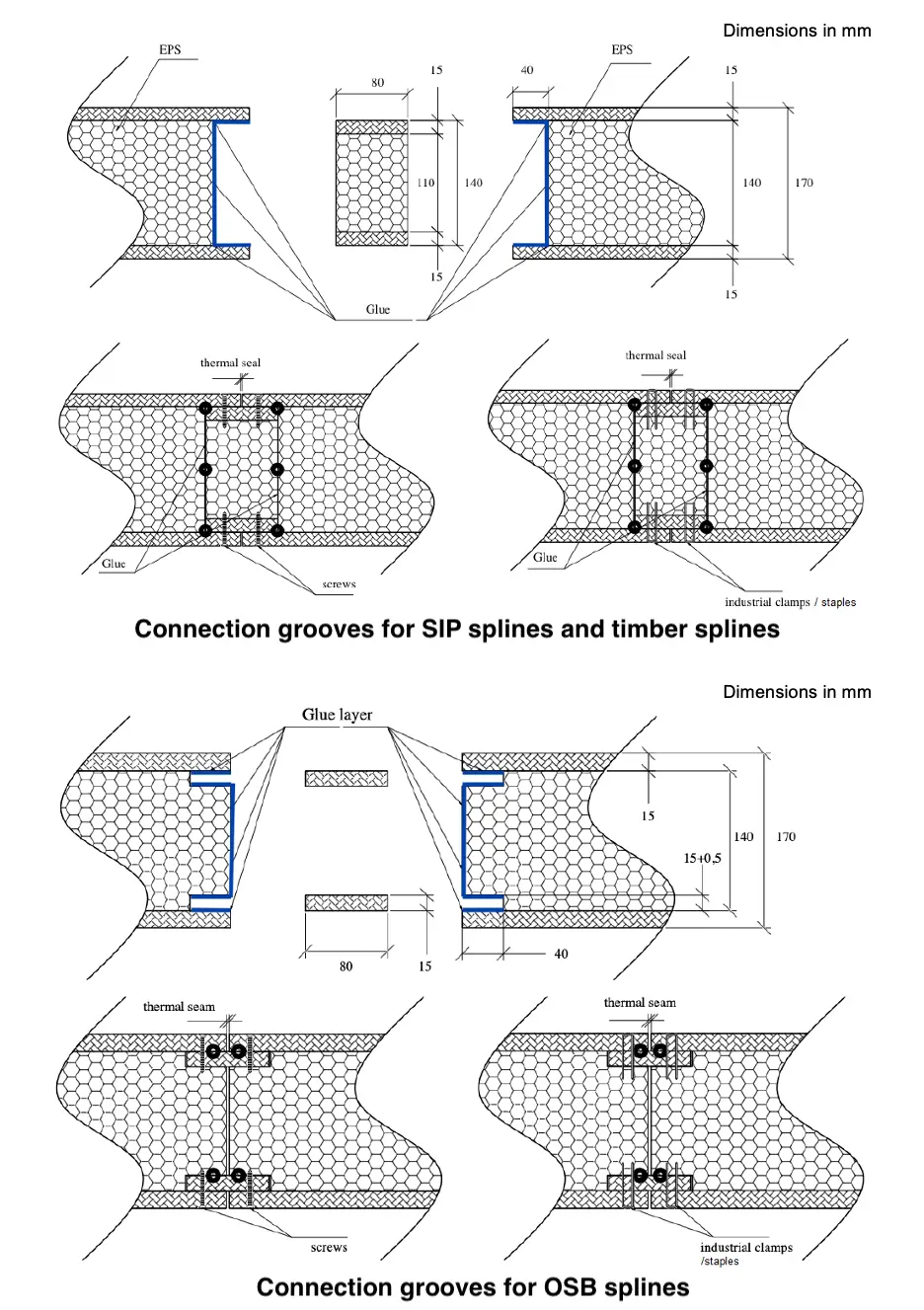
The working surface of the table is covered with stainless steel, ensuring durability and easy cleanup. The machine is equipped with an electric brake system and a mechanical hand protection system, ensuring safety during operation. The grooving parameters are set on the control console, streamlining the setup process and ensuring accuracy.
EPS boards cutting process
All the materials, except EPS boards, are delivered in ready-to-use condition. EPS boards are made from EPS blocks because most of the EPS board suppliers can not guarantee the thickness accuracy of the EPS boards, and we need to cut the blocks ourselves before gluing the panels.
The thickness of the EPS boards is equal to the thickness of the connection timber/element plus 2 mm.
If a connection element is 140 mm thick, the EPS board must be 142mm to insert a connection element into the panel.
We can offer two types of machinery:
Jumbo-SIP assembling process
Jumbo-SIP—these are what we call big panels, used as completed walls, floors, or roof panels. Sometimes, increasing the number of production processes in the factory is economically effective, and Gluestream develops prefab house technology.
We can offer many types of assembling tables, flipping and tilting tables, conveyors, and manipulators.