Was ist ein SIP-Paneel-Konstruktionssystem?
SIPs, also known as structural-insulated panels, became popular as an energy-efficient building material even in the middle of the last century. They comprise two outer layers of oriented strand board (OSB), MgO boards or GFB (gypsum fiber boards), with a foam core in between. The foam core is usually made of expanded polystyrene (EPS) and polyurethane (PUR), providing excellent insulation properties.
Was sind die Vorteile des SIPs-Baus?
- Außergewöhnliche Energieeffizienz: Sandwichpaneele sind so konzipiert, dass sie eine hervorragende Isolierung bieten, die Energiekosten senken und komfortablere Lebensbedingungen schaffen.
- Ausgezeichneter struktureller Halt, bewiesen durch ETAG.
- Faster construction times. SIP panels are pre-fabricated, and the house can be quickly assembled on-site, reducing time, labor costs, and other fees.
- Der SIPs-Produktionsprozess erzeugt weniger Abfallmaterialien als traditionelle Methoden. Sandwichpaneele werden aus Materialien hergestellt, die keine schädlichen Gase oder Chemikalien freisetzen.
- Strukturierte Isolierpaneele können verwendet werden, um eine Vielzahl moderner Bauideen zu verwirklichen. Sie können sowohl für Wohnhäuser als auch für Gewerbeimmobilien verwendet werden und erfüllen die spezifischen Anforderungen des Projekts.
Um die Produktion zu starten und wettbewerbsfähiger zu sein, müssen Sie professionelle Maschinen für die hochwertige SIP-Herstellung kaufen. Wir sind ein erfahrener Lieferant eines kompletten Produktionssets für Sandwichpaneele und bieten Maschinen mit unterschiedlichen Automatisierungsgraden und entsprechenden Preisen an.

Das Standardmaschinen-Set besteht aus:
- Paneel-Laminier- und Pressmaschinen;
- Paneel-Schneide- und Nutmaschinen;
- Hilfsmaschinen - Hebevorrichtungen, Kernschneider, Brecher, Verpackung, Markierung und Messwerkzeuge.
Wir empfehlen die Verwendung von zwei Haupttypen von Polyurethankleber:
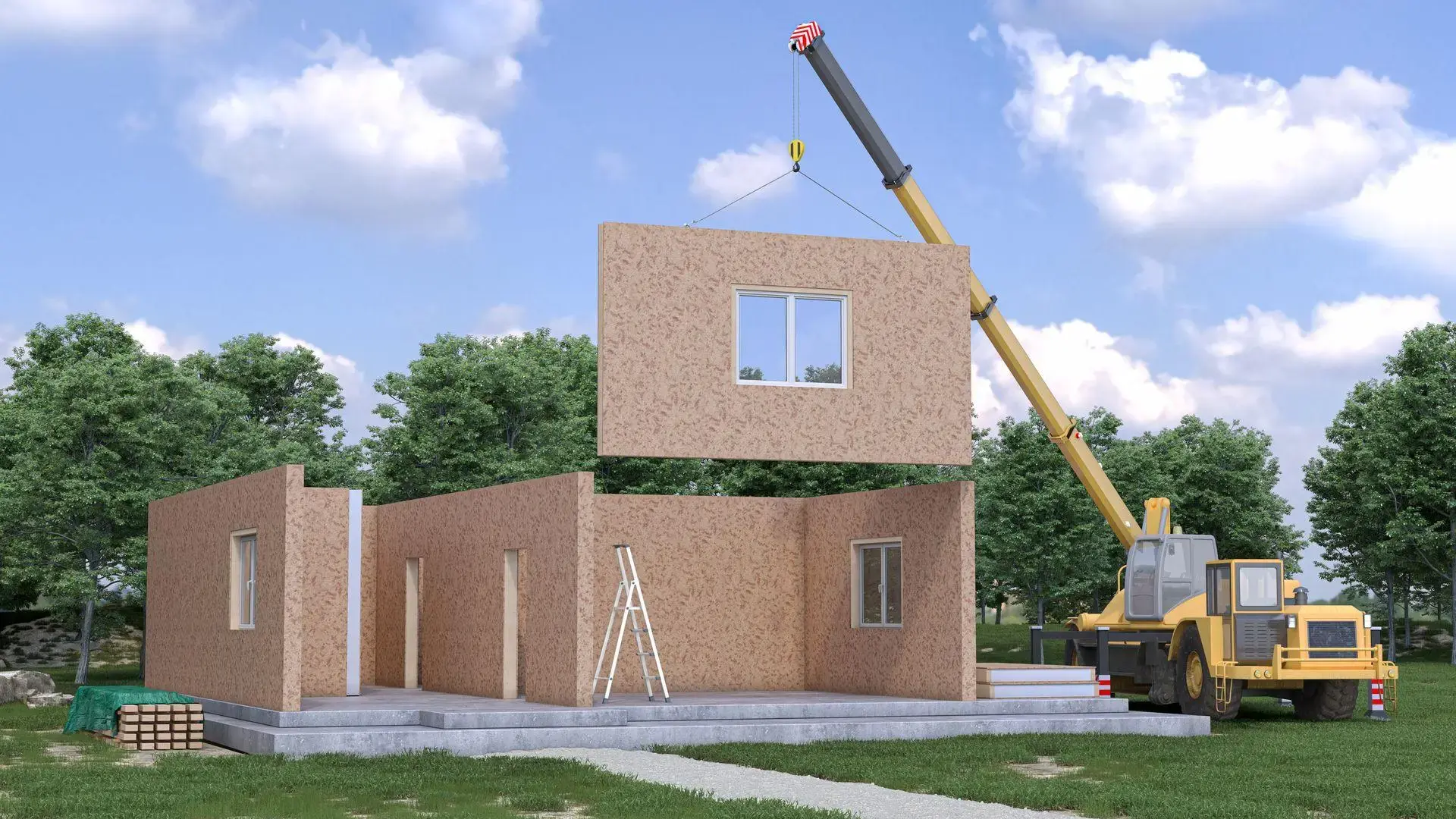
Der Herstellungsprozess von SIPs ist ein entscheidendes und komplexes Verfahren, das die hohe Qualität unserer Produkte gewährleistet. Er umfasst mehrere wichtige Schritte, die wir sorgfältig befolgen, um erstklassige Ergebnisse zu liefern:
- Das Haus entwerfen, um Klebe-, Schneide- und Montagepläne zu erstellen und die Arten der Verbindungselemente entsprechend der erforderlichen Tragfähigkeit der Wand-, Dach- oder Bodenpaneele auszuwählen.
- Materialvorbereitung und Qualitätskontrolle.
- Verkleben der Paneele;
- Schneiden der Paneele;
- Herstellung der Verbindungskanäle im Kern des Paneels;
- Markierung der Paneele gemäß dem Schneideplan und Verpackung zur Auslieferung;
Sobald das Hausbausatz produziert ist, besteht der nächste Schritt darin, das Haus zu montieren. Dies kann entweder in der Fabrik oder draußen, direkt auf der Baustelle, je nach Projektanforderungen erfolgen.
Paneel-Laminierungsprozess.
Wir möchten einige der Haupttypen von SIP-Paneel-Produktionsanlagen vorstellen, sind aber offen für die Diskussion individueller Kundenanfragen.
Die halbautomatische SIPs-Produktionslinie ist mit einer 1-C PUR-Klebstoffauftragmaschine Gluestream SPL-9 und mehreren C-Typ-Pressen ausgestattet.
Die Klebstoffauftragmaschine kann mit einer stationären oder beweglichen Plattform verwendet werden.
Die Stapel von Paneelen werden in den C-Typ-Pressen montiert. Das Entladen der Platten erfolgt mit einem Gabelstapler.
How do we calculate the production capacity of the SIP panels production line, and how do we choose the PUR glue?
One-component PUR glue has two main parameters to calculate the SIP manufacturing line’s capacity:
- OJT – Open Joint Time (max time open to air), which is the time of assembling a stack of the boards in the press.
- PT – Presszeit, die zum Pressen erforderliche Zeit.
The glue parameters are calculated if the temperature in the production facility is 20℃-25℃.
10–15 Minuten benötigen wir, um neun 170 mm dicke SIPs in der Presse zu montieren;
- wir benötigen Kleber mit 15 Min. OJT.
- PT beträgt ca. 40 Min.
Sie können einen Produktionsplan von SPL-9 mit 4 Pressen in einer 8-Stunden-Schicht sehen.
In der tatsächlichen Produktion können wir einen Reduktionsfaktor von 0,8 verwenden.
261*0,8=209 Platten pro Schicht.
Das Personal besteht aus zwei Bedienern und einem Gabelstaplerfahrer.
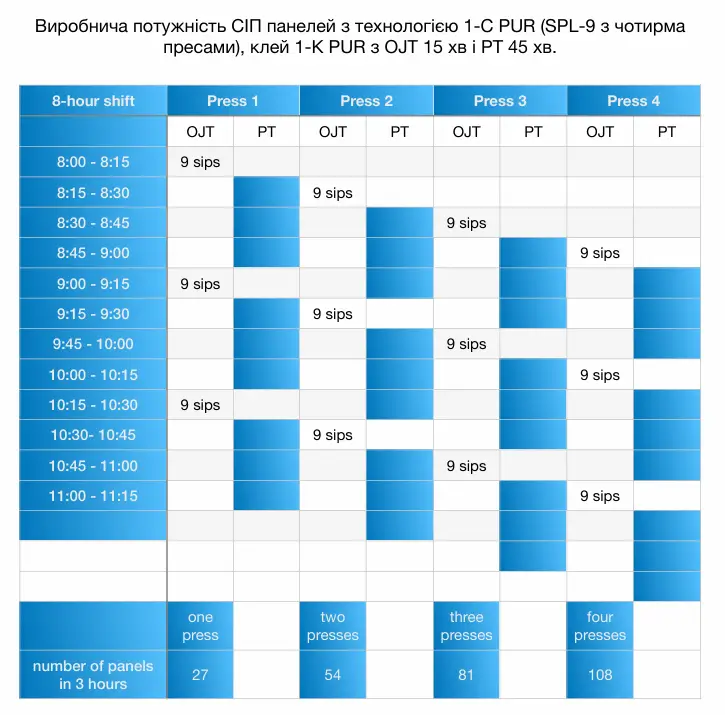
Sandwichpaneel-Produktionslinie SPL-2 mit zwei Portalpressen besteht aus den folgenden Modulen:
- Ein stationäres Klebstoff-Auftragungsportal mit automatisch angehobenem Kopf.
- Pumpstation.
- Ein beweglicher Wagen, auf dem der Stapel der Platten montiert wird.
- Zwei Portalpressen (max.).
- Der Vakuumheber wird verwendet, um Materialien auf den Wagen zu laden (optional).
- Das Entladen der Stapel erfolgt mit einem Gabelstapler.
Produktionskapazität – max. 100 Platten pro Schicht.
Personal – zwei Personen (einer ist gleichzeitig Gabelstaplerfahrer).
Wenn Sie eine geringere Produktionskapazität benötigen, ist die SIP-Produktionsmaschine SPL-1 mit einer Presse Ihre Wahl
Sandwichpaneel-Produktionslinie, SPL-10M, besteht aus den folgenden Modulen:
- Ein bewegliches Klebstoff-Auftragungsportal mit automatisch angehobenem Kopf.
- Pumpstation.
- Ein Rollenförderer mit oder ohne Scherenhubtisch.
- Eine Verteilplattform, um die Paneele in und aus den Pressen zu transportieren.
- Eine bis sechs Portalpressen.
- Ein Vakuumheber zum Laden von Materialien (optional).
- Das Entladen der Stapel erfolgt mit einem Gabelstapler.
Die Produktionskapazität beträgt 50 – 250 Platten pro Schicht, abhängig von der Anzahl der Pressen.
Personal – zwei Personen (einer von ihnen ist gleichzeitig Gabelstaplerfahrer)
SPL-10M kann auch Teil der vollautomatischen SIP-Paneel-Produktionslinie sein, die mit vier Pressen und einem automatischen Montageportal ausgestattet ist.
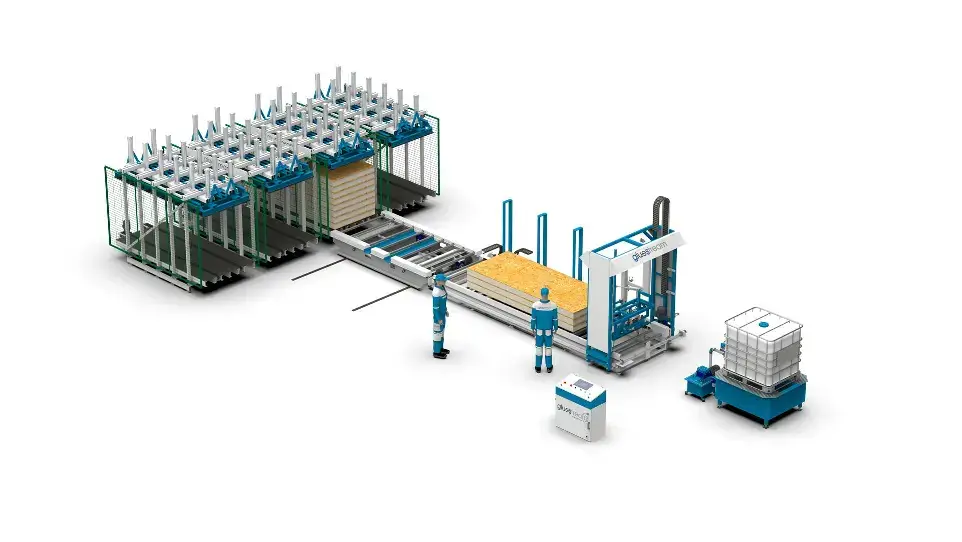
Vollautomatische Sandwichpaneel-Produktionslinie ASPL 3.1.BFT
Die Ausrüstung ist dazu bestimmt, die SIPs automatisch zu laminieren.
Jumbo-SIP-Produktionslinien
Die Absicht, so viele Prozesse wie möglich in die Fabrik zu verlagern, wird wirtschaftlich praktikabel.
Manchmal ist der Zugang zu den benötigten Materialien in Ihrer Region eingeschränkt, daher haben wir einen technologischen Prozess zur Herstellung von großformatigen SIP-Paneelen entwickelt, die in der Fabrik zur Erstellung von fertigen Wänden, Dächern und Böden verwendet werden können.
Es gibt ein paar Möglichkeiten, es zu tun.
SIPs Schneidprozess
Sobald ein Schneidplan erstellt wurde, liefert er wichtige Details zur Positionierung des Paneels auf dem Sägetisch, einschließlich der Anzahl der zu schneidenden Elemente, der Tiefe der Verbindungskanäle und der Bearbeitungswinkel. Durch das präzise Befolgen des Plans können Hersteller Materialverschwendung minimieren und die Effizienz bei der Plattenbearbeitung maximieren. Dies kann zu erheblichen Kosteneinsparungen und einer erhöhten Produktivität in der Fertigung führen.
Universelle halbautomatische SIP-Paneelsäge FPS-900
Eines der wichtigsten Werkzeuge für die Plattenbearbeitung ist die SIP-Paneelsäge FPS-900. Diese Säge ist speziell dafür ausgelegt, Paneele mit einer Dicke von bis zu 300 mm zu schneiden.
Die Säge kann für alle Schnitte von 0 bis 45 Grad verwendet werden.
Zusätzlich verfügt die Paneelsäge über ein automatisches System zur Längenmessung, das vom Bediener eingestellt wird. Diese Funktion hilft, Präzision und Genauigkeit im Prozess zu gewährleisten, Abfall zu reduzieren und die Effizienz zu verbessern.
Die Säge FPS-900 ist in zwei Modifikationen erhältlich, um die einzigartigen logistischen Anforderungen jeder Produktionsstätte zu erfüllen.
Die erste Modifikation ist FPS-900.BC.AM, verfügt über ein Förderbandsystem, das die Paneele in den Arbeitsbereich liefert und positioniert. Diese Modifikation ist mit einem automatischen Messsystem und einem Paneelpositionierungssystem ausgestattet.
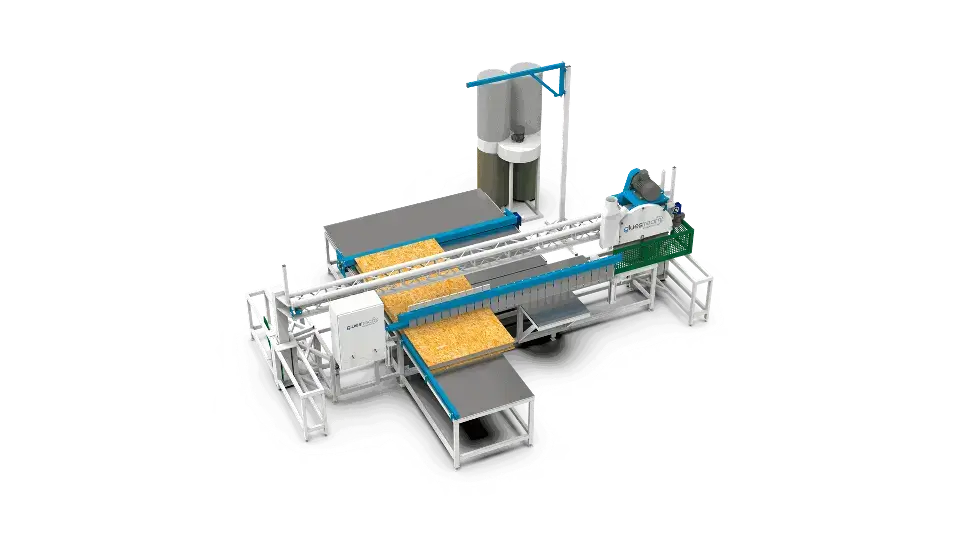
Die zweite Modifikation der SIP-Säge, FPS-900.ST.AM, verfügt nicht über ein Förderbandsystem. Stattdessen müssen die Arbeiter das Paneel manuell auf den Tisch legen und es an den Messbalken drücken, der in der Schneidposition platziert ist. Nach dem Schneiden werden die Teile der Paneele automatisch mit einem Balken in den Ladebereich zurückgeführt. Die Oberfläche des Tisches ist mit Edelstahl bedeckt, um Haltbarkeit und einfache Reinigung zu gewährleisten.
Nutenprozess von SIP-Paneelen
SIP-Paneel Nutung Maschine FPS-400 ist ein wesentliches Werkzeug zur Erstellung von Verbindungskanälen im Kern von SIPs aus Materialien wie EPS, geschäumtem PU und PIR. Jedes Set von Schneidwerkzeugen wird entsprechend den Anforderungen der Kunden und den Designs der Verbindungskanäle entworfen, um sicherzustellen, dass die Kanäle präzise und genau sind. Der Schneidkopf wird entlang präziser Führungen bewegt, und das pneumatische Spannsystem sorgt dafür, dass die Platte fest auf dem Arbeitstisch positioniert ist.
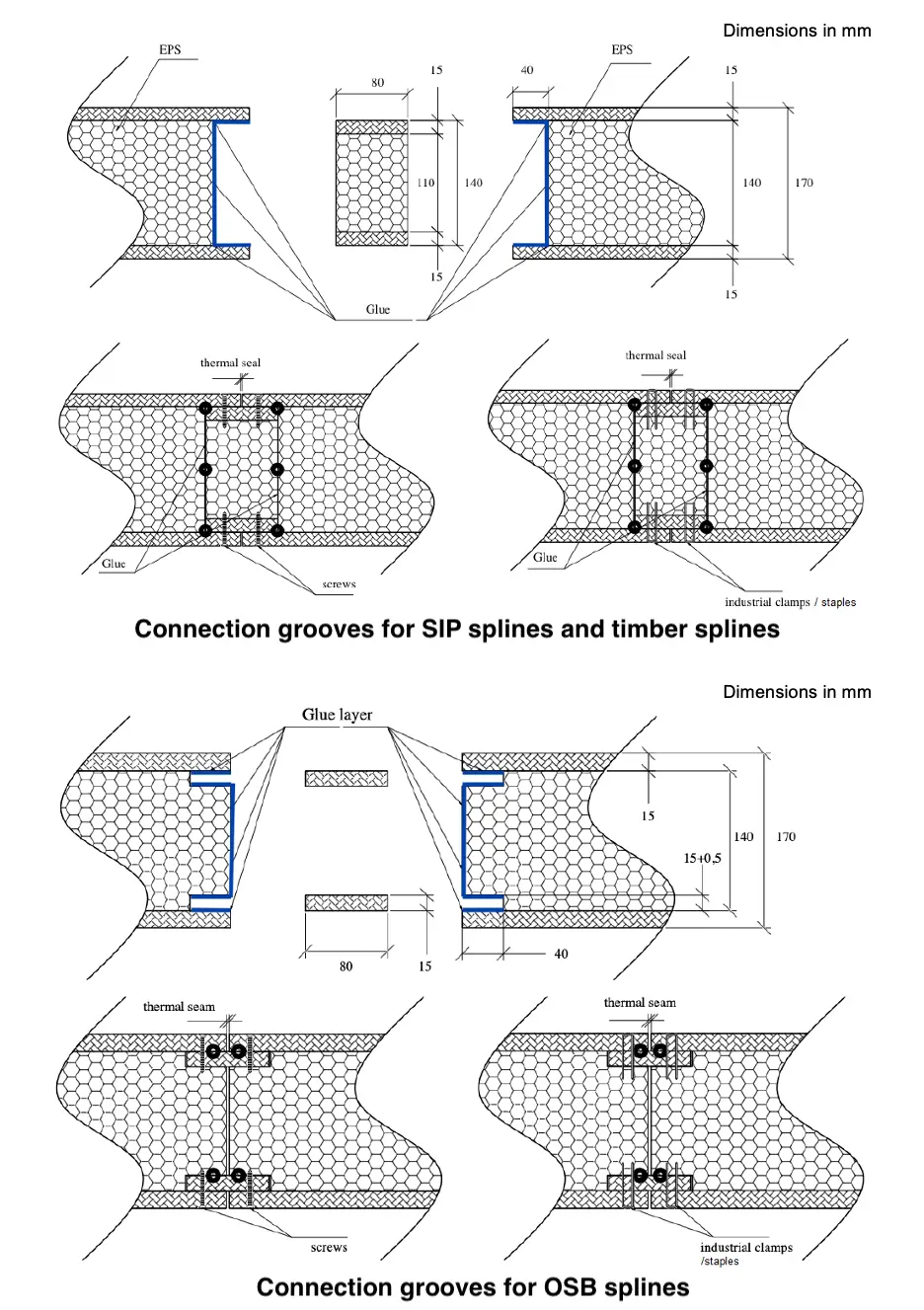
Die Arbeitsfläche des Tisches ist mit Edelstahl bedeckt, was Haltbarkeit und einfache Reinigung gewährleistet. Die Maschine ist mit einem elektrischen Bremssystem und einem mechanischen Handschutzsystem ausgestattet, um Sicherheit während des Betriebs zu gewährleisten. Die Rillenparameter werden auf der Steuerkonsole eingestellt, was den Einrichtungsprozess vereinfacht und Genauigkeit sicherstellt.
EPS-Platten Schneidprozess
Alle Materialien, außer EPS-Platten, werden gebrauchsfertig geliefert. EPS-Platten werden aus EPS-Blöcken hergestellt, da die meisten EPS-Plattenlieferanten die Dickenpräzision der EPS-Platten nicht garantieren können, und wir müssen die Blöcke selbst zuschneiden, bevor wir die Paneele verkleben.
Die Dicke der EPS-Platten entspricht der Dicke des Verbindungsholzes/Elements plus 2 mm.
If a connection element is 140 mm thick, the EPS board must be 142mm to insert a connection element into the panel.
Wir können zwei Maschinentypen anbieten:
Jumbo-SIP-Montageprozess
Jumbo-SIP—das sind die großen Paneele, die als fertige Wände, Böden oder Dachpaneele verwendet werden. Manchmal ist es wirtschaftlich effektiv, die Anzahl der Produktionsprozesse in der Fabrik zu erhöhen, und Gluestream entwickelt die Technologie für vorgefertigte Häuser.
Wir können viele Arten von Montagetischen, Kipp- und Neigetischen, Förderbändern und Manipulatoren anbieten.